About the project
Takeda developed a new high-containment production facility to manufacture its oral solid dosage oncology treatment Ninlaro® for global markets. Located at Takeda’s existing site in Dublin, Ireland, the project was Winner of an ISPE Facility of the Year Category Award for Facility Integration.
A highly configurable and flexible facility
This integrated building is unique in that it houses all steps of the production process including API, Drug Product, Primary and Secondary packaging and QA/QC Laboratory processes, under one roof.
The facility was designed to meet the regulatory requirements for the sale of product worldwide. It was designed to be configurable and flexible.
It provides for the manufacture of chemical synthesis steps including Reaction, Liquid/Liquid Extraction, Separation, Distillation and Filtration steps. These synthesis processes include additions in both solid and liquid phases. Containment levels below 100 ng/m3 are required for many of the steps. This necessitated the design of primary and secondary containment solutions.
Materials handling solutions include isolator technology, split butterfly valves and flexible isolators located throughout the facility (API, DP, Packaging and QC laboratories). Contained waste handling solutions are incorporated in the design for the handing of contaminated waste streams.
Design innovation
The building has large glazed sections both on the exterior and within. This allows high levels of natural daylight into each room, providing an enhanced working environment. A visitors viewing corridor facilitates visibility of the manufacturing operations from outside the GMP / high containment manufacturing areas.
Small scale equipment and product operations were facilitated by the use of RTP based handling in API and DP areas, along with selective use split valve canister transfers. A range of liquid charge solutions were developed for handling the accurate dispensing and charge of hazardous liquids.
State-of-the-art laboratory
A QA/QC laboratory contains high containment isolator technology integrated with hybrid isolators and fume cupboards. These are for the handling and testing of intermediate and final product samples.
“The application of good design practice and great conceptual planning led to the excellent integration of facility and process in this development," said Andy Rayner, Pharma Sector Director
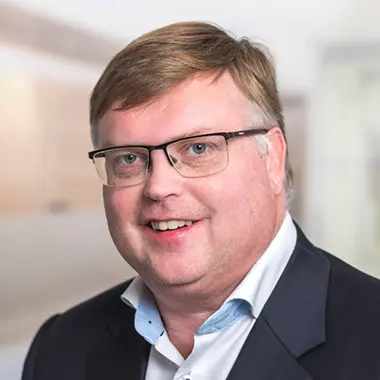
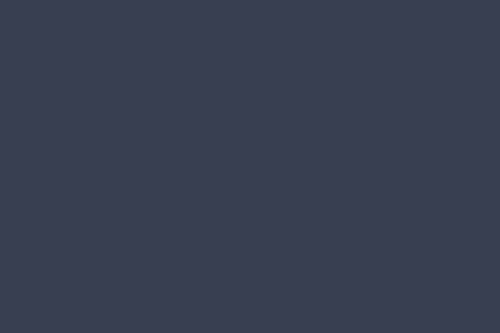
"The innovative design as an ‘all-in-one’ facility incorporates the entire end-to-end production process from API to drug product and packaging under one roof."
Andy Rayner
Executive Director
Our Services
PM Group’s multi-disciplinary team, including specialists in API and DP manufacturing and process containment, completed the detailed design, equipment and contract procurement services and regulatory submissions.
PM Group were appointed as Construction Managers for the facility build phase. We also provided Commissioning, Qualification and Validation (CQV) services.
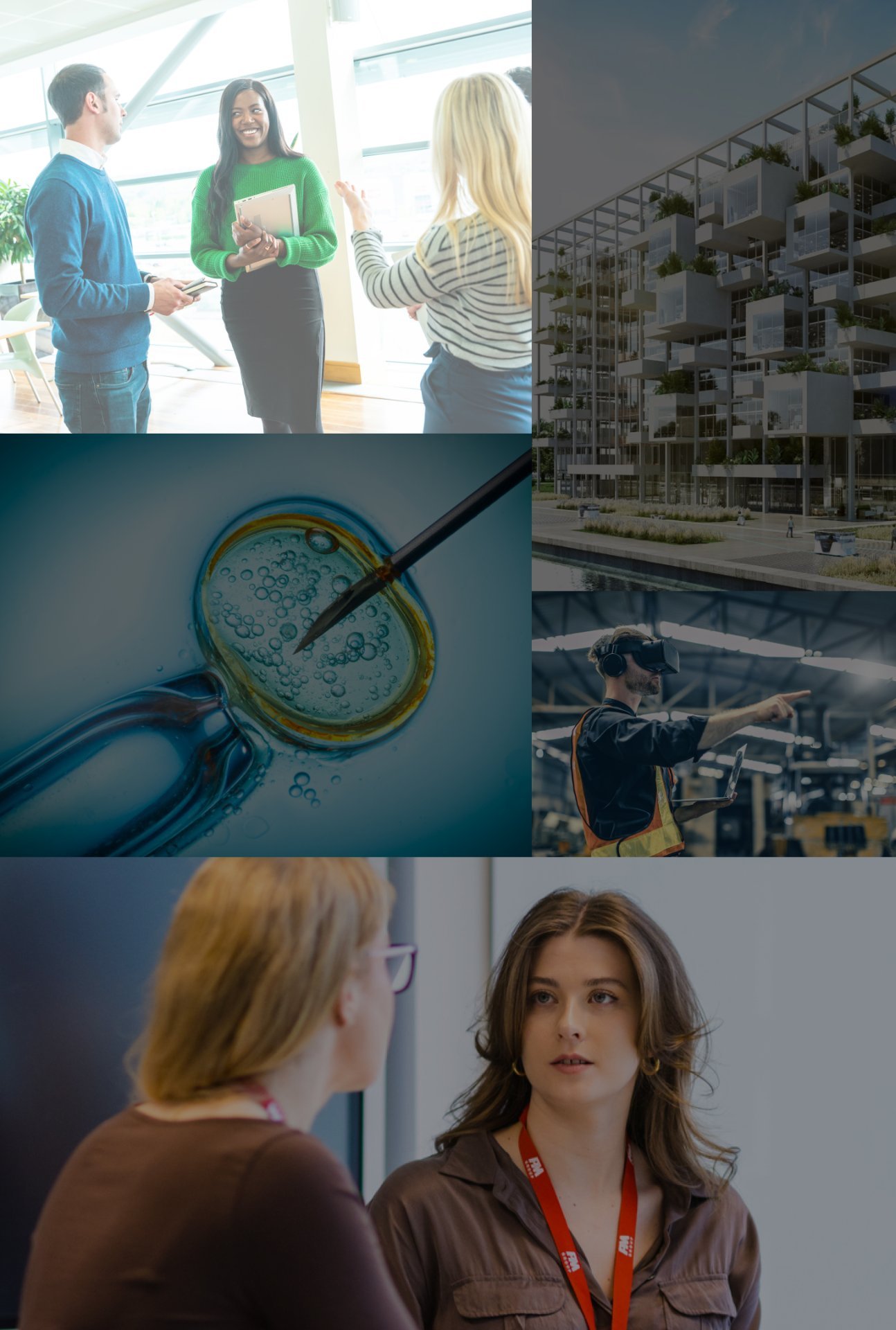
Contact Us
Thanks for your enquiry, we’ll be in touch presently.
In the meantime you may find this content relevant to your interests.